Canoe Building 101
The Basics of an Anishinaabe Birchbark Canoe
by Natalie Lopez
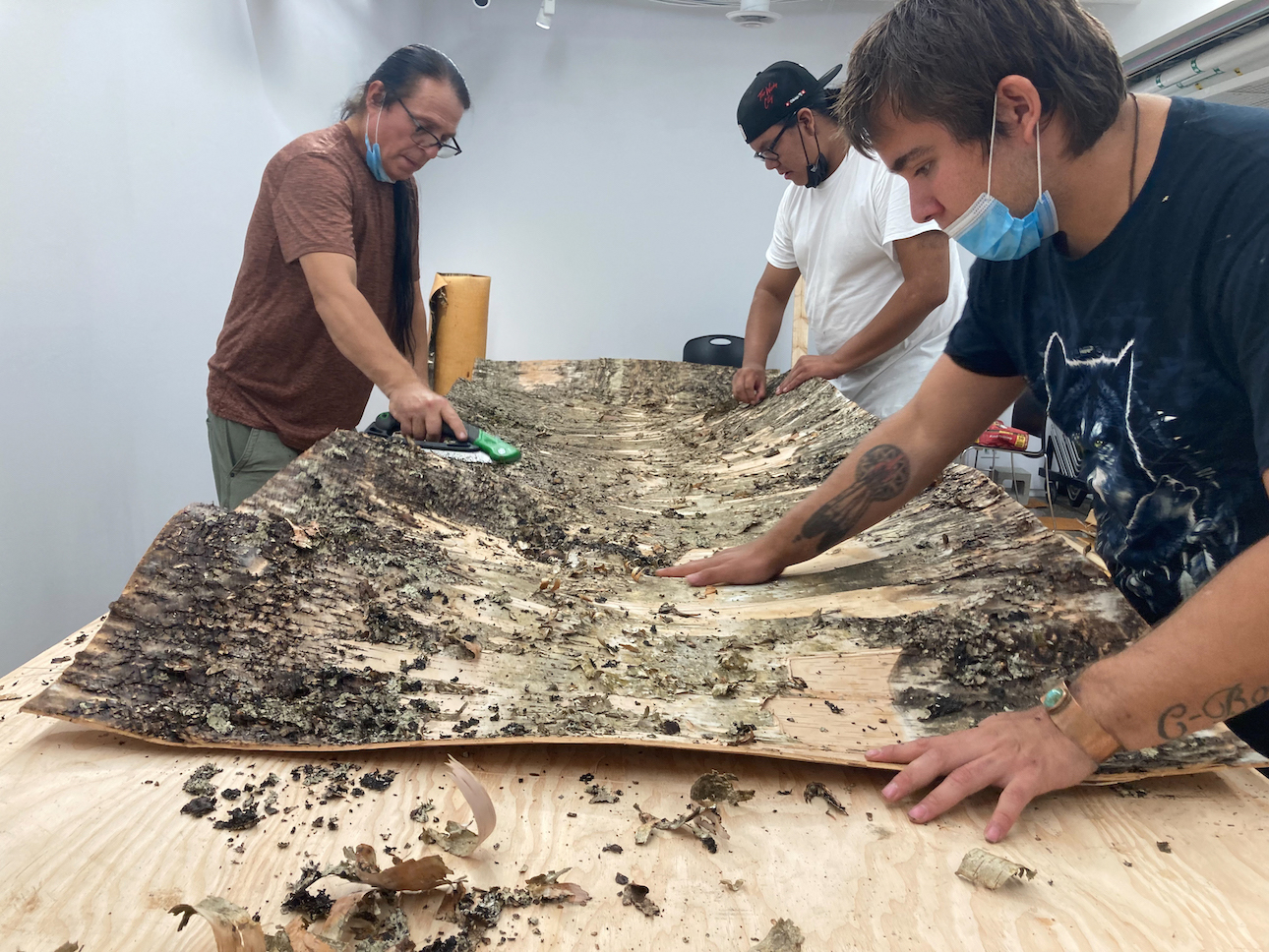
Three main processes take place when building an Anishinaabe traditional birchbark canoe, according to Valliere. The first is locating the materials, which involves going into the forest and identifying which trees will eventually become the canoe. Valliere said that a tree has to have a diameter of 16 to 18 inches and a specific thickness that can be conveyed by the distance between the eyes on the lines of the bark.
Over the summer, Northwestern third-year graduate student in the learning sciences program, Forrest Bruce, who is Ojibwe, was invited to Lac du Flambeau to harvest materials with Valliere this past summer. Bruce said there were four days of harvesting, on the first day they drove to an old logging road to gather spruce root from trees that were marked to be cut for lumber.
Valliere’s mastery in canoe building also involves knowing the best places to harvest, Bruce said.
“He just has a really deep knowledge of that place, and knows a lot of different trees and plants and the best kind of places to go harvest something,” Bruce added.
The second process in canoe building is processing these materials into usable elements of the canoe. The best time to do this is in the spring and summer when the bark most easily peels off the tree. The spruce roots that will later be used to bind the canoe need to be pulled from the ground, the bark of the birch trees needs to be peeled off using a bark disk or by hand, the cedar needs to be split before it can be carved to form the ribs and frame of the canoe. In this step, all of the components are made and prepared first before they are assembled into the canoe.
During the harvesting of materials, it’s important that respect is shown to the forest. Before any harvesting is done, Valliere prays for every piece of material, asks for permission to take from the forest, and says thank you. When harvesting the birchbark, it must be done in a way that will not kill the tree.
“That’s all part of Indigenous knowledge. Just having that place-based knowledge, and knowing where to go to find those things and how to harvest them in a respectful and sustainable way,” Bruce said.
Once the materials have been harvested and prepared, the third and final process is the construction of the canoe. Birchbark, which is waterproof on the inside, forms the hull of the canoe, while the ribs and frame are made of cedar. Spruce roots are trimmed, peeled, and split so they can be used to stitch the canoe together. All of the materials are soaked in water in order to make it pliable.
Valliere and his apprentices began the construction process by building a work table for the canoe to be placed on. By the second day, the canoe form was finished and ready to be covered in birchbark. Boiling water was poured on the bark in order to make it more pliable to fit the curves of the canoe. Next came the process of sewing the canoe together with the soaked spruce roots. The ribs were soaked, formed to fit the canoe, and then trimmed. The birchbark canoe was finished once it was sealed with pitch (a waterproof sealant made from spruce pitch and charcoal) to prevent any leakages.
“There are wood tolerances and curves on this canoe that you can’t use a protractor to find. It can only be found by sight and touch and feel,” said Valliere.
During the construction process, the measurements of the canoe are taken by the body measurements of humans. Valliere described the width of the canoe to be 35 inches because it’s the same length if a man held his arms out and measured from elbow-to-elbow. The height of the front bow is the same length as the tip of a finger to the bottom of the elbow, while the width of the ribs is the width of a hand.
“At a certain point, you can’t really measure the dimensions of the canoe exactly. You have to do it kinda by feel,” said Bruce.
All these processes combined produce an Anishinaabe birchbark canoe, along with so much more, as Valliere brings with him knowledge and lessons that unify the people around him,
“Canoe building helps bring people together,” Valliere said.
Back to articles